-
Differential Pressure Gauge
-
Digital Pressure Gauge
-
Stainless Steel Pressure Gauge
-
Precision Pressure Transmitter
-
Programmable Logic Controller
-
Float Level Switch
-
Pneumatic Valve Positioner
-
Temperature Transmitter Sensor
-
Hart Field Communicator
-
Solenoid Valve
-
Control Valves
-
High Accuracy Flow Meter
-
Submersible Water Pump
-
Pressure Transmitter Manifold
-
Ultrasonic Level Meter
-
Voltage Current Power Meter
8 VDC Sick Hengstler Encoder IP40 1gcm² RoHs Stainless Steel
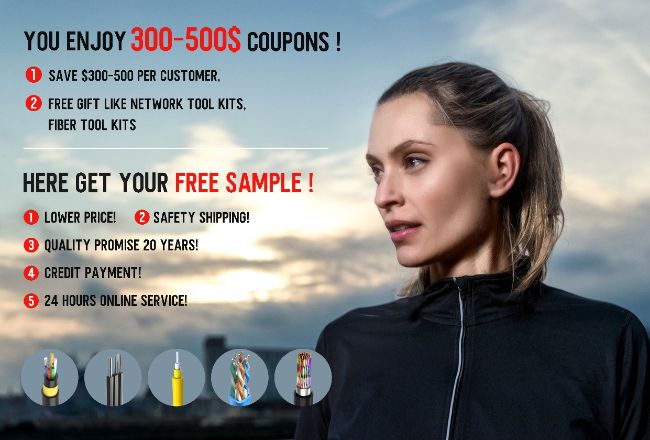
Contact me for free samples and coupons.
Whatsapp:0086 18588475571
Wechat: 0086 18588475571
Skype: sales10@aixton.com
If you have any concern, we provide 24-hour online help.
xSupply Voltage | 7 V DC ... 12 V DC | Power Consumption | < 50 MA |
---|---|---|---|
Weight | ≤ 0.05 Kg | Moment Of Inertia Of The Rotor | 1 Gcm² |
Enclosure Rating | IP40 | Recommended Supply Voltage | 8 V DC |
Highlight | 8 VDC Sick Hengstler Encoder,Sick Hengstler Encoder IP40,IP40 hengstler absolute encoder |
Sine/cosine periods per revolution | 16 | |
---|---|---|
Number of the absolute ascertainable revolutions | 1 | |
Maximum number of steps per revolution | 512 via RS485 | |
System accuracy | ± 432 ″ | |
Supply voltage | 7 V DC ... 12 V DC | |
Recommended supply voltage | 8 V DC | |
Power consumption | < 50 mA | |
Weight | ≤ 0.05 kg | |
Moment of inertia of the rotor | 1 gcm² | |
Operating speed | 12,000 min⁻¹, 12,000 U/min | |
Angular acceleration | ≤ 500,000 rad/s² | |
Permissible radial shaft movement | ± 0.15 mm | |
Permissible axial shaft movement | ± 0.3 mm | |
Operating temperature range | –40 °C ... +115 °C | |
Storage temperature range | –50 °C ... +125 °C | |
Relative humidity/condensation | 90 % | |
Resistance to shocks | 100 g, 10 ms, 10 ms (according to EN 60068-2-27) | |
Frequency range of resistance to vibrations | 50 g, 10 Hz ... 2,000 Hz (according to EN 60068-2-6) | |
EMC | According to EN 61000-6-2 and EN 61000-6-3 1) |
100% original and new Sick Hengstler Encoder SEK37-HFB0-S01 0.05 kg < 50 mA ± 432 ″high accuracy
Product description
The SEK/SEL37 capacitive motor feedback systems are from two different automation worlds: On the one hand, the world of resolvers, where users require more power from absolute final encoders, such as with servo motors or feeder axes. On the other, the SEK/SEL37 devices are particularly interesting for servo motor manufacturers due to the flexibility in connection with the automation technology features. With 16 sine/ cosine signals per revolution, this family represents the basic solution among the MFB systems with HIPERFACE® interface. The centerpiece of the product.
Specification
Moment of inertia of the rotor | 1 gcm² |
Weight | ≤ 0.05 kg |
Permissible radial shaft movement | ± 0.15 mm |
Operating temperature range | –40 °C ... +115 °C |
Enclosure rating | IP40 |
Recommended supply voltage | 8 V DC |
At a glance
• Motor feedback systems for the basic performance range
• 16 sine/cosine periods per revolution
• Absolute position with a resolution of 512 increments per revolution and 4,096 revolutions with the multiturn system
• Programming of the position value
• Electronic type label
• HIPERFACE® interface
• Installed version with tapered shaft and axial or radial connector outlet
• Conforms to RoHs
Your benefits
• The small dimension allows manufacturers of low-power and minimalpower motors to considerably reduce the size of their motors
• The SEK/SEL37 motor feedback systems are excellently suited for use under rough environmental conditions
• The capacitive principle of measurement with holistic scanning allows for high axial and radial tolerances
• The consistent mechanical components in SKS/SKM36 allow for a high degree of flexibility with various encoder systems
NOTICE
In order to receive safety-related position or speed information when using encoders or motor feedback systems, a fault exclusion is required for the mechanical coupling on the drive shaft or additional measures must be taken. The motor feedback system only contributes to the protective function when used in servo systems in connection with drives. The connected drive must feature measures designed to achieve a safe status. Addi‐ tional protective devices and measures may be necessary for the motor feedback system. Implementing a safety function supported by the encoder requires a suitable evaluation unit (e.g. programmable logic controller, machine controller). The encoder is unable to bring the machine/system into a safe status on its own. The suitable evaluation unit must feature meas‐ ures designed to achieve a safe status. Additional protective devices and measures may be necessary in addition to encoders. The safety level of the motor feedback system or encoder must be compatible with the safety level of the motor or the machine/system (for the motor feedback system and encoder safety level, see the type label)
Angular measurement error
In order to calculate the angular measurement error, the measured angular values from one turn of the device under test and the reference encoder of the test system are subtracted from each other. The resulting angular measurement error consists of both systematic and random error components. The example in the graph shows systematic error components of 32 physical periods per turn, a single period error as well as statistical noise. The measured systematic error excluding the noise has to be within the datasheet error limit, which is given as the symmetrical maximum deviation from the real mechanical angle of the reference encoder. This real angle can be understood as an angular position relatively depending on the application’s angular zero or commutation, which can be adjusted by applying a position offset